X-Hab 2025 NASA Proposal: Difference between revisions
Acmattson3 (talk | contribs) Updated for relevancy. |
Acmattson3 (talk | contribs) No edit summary |
||
Line 9: | Line 9: | ||
<ul> | <ul> | ||
<li><strong>Long-Term Vision:</strong> Transform the solar system using robotic construction with local materials.</li> | <li><strong>Long-Term Vision:</strong> Transform the solar system using robotic construction with local materials.</li> | ||
<li> | <li><strong>Short-Term Vision:</strong> Robotic construction of Artemis Base Camp.</li> | ||
<li><strong>Mission:</strong> Design and demonstrate robots capable of autonomously constructing Artemis Base Camp structures using locally sourced Lunar regolith, focusing first on an arch-based, regolith-covered vehicle bay.</li> | <li><strong>Mission:</strong> Design and demonstrate robots capable of autonomously constructing Artemis Base Camp structures using locally sourced Lunar regolith, focusing first on an arch-based, regolith-covered vehicle bay.</li> | ||
</ul> | </ul> | ||
<h2> | <h2>Requirements</h2> | ||
<ul> | <ul> | ||
<li> | <li>The structure must allow a 2.6m x 2.6m vehicle to fit inside. (I.0)</li> | ||
<li>< | <li>Structural elements must not exceed 2.0 meters for ease of transport. (I.1.1)</li> | ||
<li>< | <li>The structure must support a regolith simulant (snow) coating of at least 0.2m thickness to simulate radiation and thermal protection. (O.0)</li> | ||
<li>The structure must tolerate a compressive load of 300 kgf and demonstrate a safety factor of at least 2. (I.1.2, I.2.1)</li> | |||
<li>Assembly must be robotically achievable, with all tools having a path to robotic automation. (E.0, E.2)</li> | |||
</ul> | </ul> | ||
<h2> | <h2>Concept of Operations</h2> | ||
<p>The design features a Lunar Autonomous Modular Platform (LAMP) robot performing the following tasks:</p> | |||
<ul> | <ul> | ||
<li> | <li>Excavation and site preparation using a bucket and grinder.</li> | ||
<li> | <li>Logistics support via part removal and transport using a forklift attachment.</li> | ||
<li>Assembly and alignment of structural components using pin-based connectors and manipulators.</li> | |||
<li>Backfilling with regolith simulant using robotic tools like snowblowers.</li> | |||
</ul> | </ul> | ||
<h2> | <h2>Key Project Goals</h2> | ||
<ul> | <ul> | ||
<li> | <li><strong>Radiation Protection:</strong> Shield against harmful cosmic rays for long-duration crew stays.</li> | ||
<li> | <li><strong>Thermal Insulation:</strong> Mitigate temperature swings during lunar day and night.</li> | ||
<li> | <li><strong>MMOD Protection:</strong> Protect from micrometeoroids and orbital debris.</li> | ||
<li><strong>Scalability:</strong> Demonstrate large-scale, robot-built infrastructure on the Moon.</li> | |||
</ul> | </ul> | ||
<h2>Project Phases</h2> | <h2>Project Phases</h2> | ||
<ol> | <ol> | ||
<li><strong>Design:</strong> | <li><strong>Preliminary Design Review (PDR):</strong> November 15, 2024 ([https://spacegrant.org/xhab/ M2M X-Hab Schedule])</li> | ||
<li><strong> | <li><strong>Critical Design Review (CDR):</strong> January 17, 2025</li> | ||
<li><strong> | <li><strong>Progress Checkpoint:</strong> March 7, 2025</li> | ||
<li><strong>Final Demonstration:</strong> May 2025</li> | |||
</ol> | </ol> | ||
<h2> | <h2>Baseline Design Solution</h2> | ||
< | <ul> | ||
< | <li><strong>Structure:</strong> Flat truss segments for modular assembly.</li> | ||
<li><strong>Materials:</strong> Durable, lightweight components pre-covered with mixed wire and cloth for ease of regolith application.</li> | |||
<li><strong>Robot:</strong> Modular LAMP robot for excavation, assembly, and backfilling.</li> | |||
<li><strong>Performance:</strong> High load-bearing capacity with a safety factor of at least 2.</li> | |||
</ul> | |||
<h2> | <h2>Verification and Testing</h2> | ||
<ul> | <ul> | ||
<li> | <li>Destructive and nondestructive compressive load tests.</li> | ||
<li> | <li>Full-scale assembly and snow load testing in a controlled environment.</li> | ||
<li> | <li>Robot alignment and assembly demonstration in a lab setting.</li> | ||
</ul> | </ul> | ||
<h2>Educational Integration</h2> | <h2>Educational Integration</h2> | ||
<p>The project | <p>The project integrates into UAF's curriculum, offering hands-on systems design and testing opportunities for engineering students.</p> | ||
<h2>Additional Information</h2> | <h2>Additional Information</h2> | ||
<p>For more details, please contact Dr. Orion Lawlor at oslawlor@alaska.edu.</p> | <p>For more details, please contact Dr. Orion Lawlor at oslawlor@alaska.edu or visit the [https://spacegrant.org/xhab/ NASA X-Hab Challenge website].</p> |
Latest revision as of 14:46, 21 December 2024
This is a stub. You can help by expanding it.
Overview
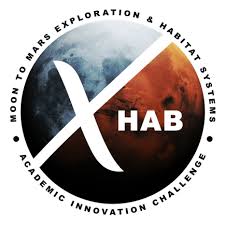
In early 2024, NASA released a request for proposals addressing the construction of a permanent lunar base. Dr. Orion Lawlor led the Aurora Robotics Team's proposal in response to Appendix B of the NASA RFP document, sponsored by NASA's Autonomous Robotic Construction Projects - TLT, PASS, ARMADAS. The proposal outlines the development of a modular robot capable of autonomous construction on the lunar surface.
Project Vision and Mission
- Long-Term Vision: Transform the solar system using robotic construction with local materials.
- Short-Term Vision: Robotic construction of Artemis Base Camp.
- Mission: Design and demonstrate robots capable of autonomously constructing Artemis Base Camp structures using locally sourced Lunar regolith, focusing first on an arch-based, regolith-covered vehicle bay.
Requirements
- The structure must allow a 2.6m x 2.6m vehicle to fit inside. (I.0)
- Structural elements must not exceed 2.0 meters for ease of transport. (I.1.1)
- The structure must support a regolith simulant (snow) coating of at least 0.2m thickness to simulate radiation and thermal protection. (O.0)
- The structure must tolerate a compressive load of 300 kgf and demonstrate a safety factor of at least 2. (I.1.2, I.2.1)
- Assembly must be robotically achievable, with all tools having a path to robotic automation. (E.0, E.2)
Concept of Operations
The design features a Lunar Autonomous Modular Platform (LAMP) robot performing the following tasks:
- Excavation and site preparation using a bucket and grinder.
- Logistics support via part removal and transport using a forklift attachment.
- Assembly and alignment of structural components using pin-based connectors and manipulators.
- Backfilling with regolith simulant using robotic tools like snowblowers.
Key Project Goals
- Radiation Protection: Shield against harmful cosmic rays for long-duration crew stays.
- Thermal Insulation: Mitigate temperature swings during lunar day and night.
- MMOD Protection: Protect from micrometeoroids and orbital debris.
- Scalability: Demonstrate large-scale, robot-built infrastructure on the Moon.
Project Phases
- Preliminary Design Review (PDR): November 15, 2024 (M2M X-Hab Schedule)
- Critical Design Review (CDR): January 17, 2025
- Progress Checkpoint: March 7, 2025
- Final Demonstration: May 2025
Baseline Design Solution
- Structure: Flat truss segments for modular assembly.
- Materials: Durable, lightweight components pre-covered with mixed wire and cloth for ease of regolith application.
- Robot: Modular LAMP robot for excavation, assembly, and backfilling.
- Performance: High load-bearing capacity with a safety factor of at least 2.
Verification and Testing
- Destructive and nondestructive compressive load tests.
- Full-scale assembly and snow load testing in a controlled environment.
- Robot alignment and assembly demonstration in a lab setting.
Educational Integration
The project integrates into UAF's curriculum, offering hands-on systems design and testing opportunities for engineering students.
Additional Information
For more details, please contact Dr. Orion Lawlor at oslawlor@alaska.edu or visit the NASA X-Hab Challenge website.